Tread
Casting
By
Dewey H.
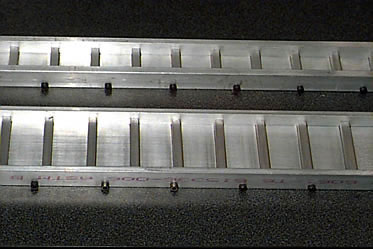
The
molds are 4 feet long and made from aluminum. They must be sprayed
with a mold release before casting.
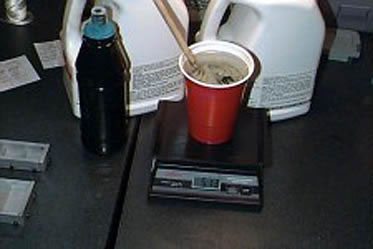
The chemicals to make the rubber must be measured precisely with
a digital scale. There is only a 2% error rate allowed before the
rubber won't galvanize. The black pigment is added after the chemicals
are mixed.
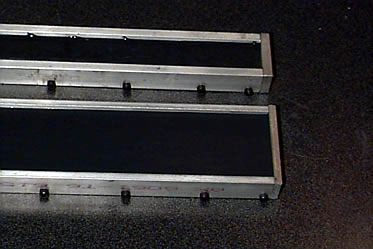
The
rubber is poured just enough to cover the ribs of the mold. The
molds must then be bounced several times to remove any air bubbles.
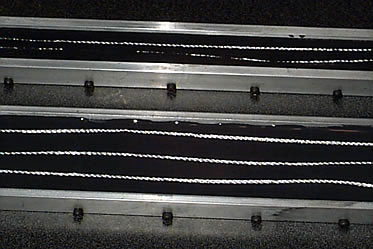
After the rubber reaches it's gel time (the point where it is no
longer a liquid) nylon cording is placed along the length of the
molds.
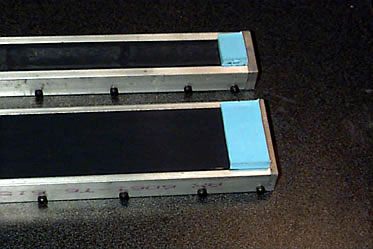
Silicone pads are then placed on all ends of the molds. These will
allow the next attached casting's nylon cording an overlap area.
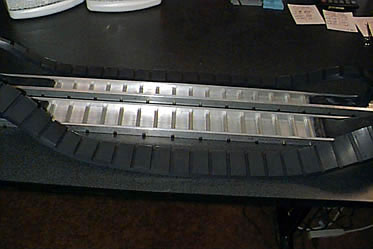
Rubber is then poured to the level mark once the silicone plugs
are in place.
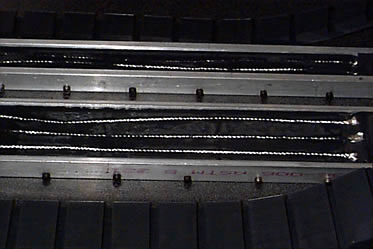
Once the rubber is set (12 to 24 hours) the treads are removed and
reset into the mold. This is where the sizing can be varied.
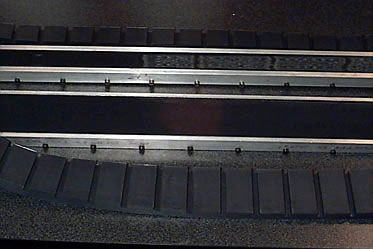
The same procedure is followed as in the first two steps with the
nylon cording run also into the areas that the silicone plugs were
in. This gives strength to the "butt splice" where the
ends meet.
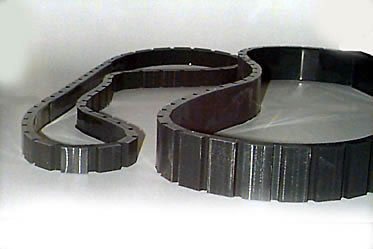
The treads are now complete. They are treated with a rubber preservative
before installing. New rubber has a tendancy to be slightly sticky
until treated. Full curing takes several days.
|