Lifter
Casting
By
Dewey H.
The
supplies to make a bubble lifter include a master from which a mold
is made, silicone rubber, catalyst, pigment, and a good digital
scale.
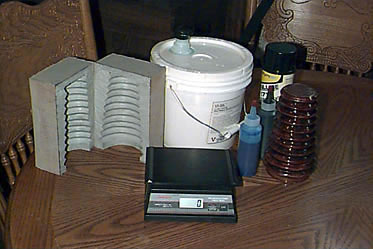
The chemicals must be mixed and weighted precisely or the rubber
will not set and ruin your mold.
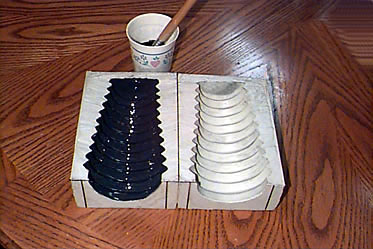
The
first step is to "paint" the silicone inside of the mold
to ensure no bubbles appear in the final product. This is call the
impression coat.
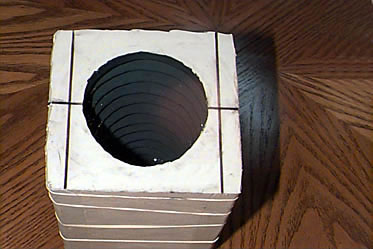
The
mold halves are then joined together.
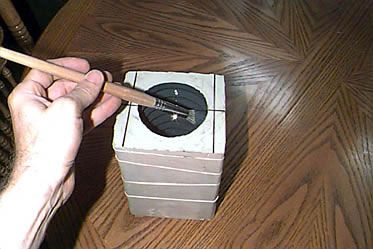
After
the impression coat dries the inside of the mold is then "painted"
two more times with fresh silicone rubber to build thickness and
strength.

After
the silicone coats dry (about 8 hours each coat) the lifter can
be carefully removed from the mold. Small plastic rings are added
inside the ribs to allow smooth collapsability.
NOTE:
Although casting the bubble lifter is relatively easy, getting to
that point can be quite complicated for the average builder with
no experience in mold making. The master must be perfect if casting
with rubber since there can be no patching up after the cast is
pulled from the mold. The chemicals that make the rubber mold must
be precisely measured and mixed. Most rubbers only allow a 3% error
before the rubber won't set at all. Silicone rubber can be expensive
also at about $110 per gallon but for this project it is perferred
because of it's coating properties and strength. Overall this project
requires above average skills to complete.
|