Claw
Construction
By
Mark W (B9-0135)
Making
the Claws from Scratch
I was always
afraid of this part of the project, and I was convinced that making
the claws on my own would be extremely difficult. It turned out
to be MUCH easier than I thought. If you are making your own or
find other ways that work better, please email me at: markweesb9@cs.com
I’m sure
that this is not the best way to make claws, but it is one way to
do it. Remember that Bill K. is the claw EXPERT. If you are not
bent on making every B9 part on your own, buy a set of Bill and
Rod’s claws. If you want to make your own, here is how I did
it.
Materials
4 pieces of
3” x 10” x 1” Birch Plywood (3/4” laminated
to ¼”)
Scroll Saw or
Jigsaw
Bench Sander
Drill Press
with Drum Sander
Wood Putty
Sandable wood
sealer
Bondo Glazing
Putty (for finishing)
Duplicolor Filler
Primer (for finishing)
A hint
to start:
Do all of your sanding at the same time for each step. If you forget
to shape an angle and have to come back to it later, it will be
hard to get the angle to match the others that you have done. (Take
it from me – I have made this mistake LOTS of times!)
1) Make the
Pattern:
I used the Dave
Painter blueprints, an “old version” Bill K. claw, and
several photos of the claws to create a pattern for the claw which
I cut from styrene.
2) Trace the
Pattern 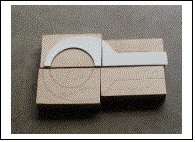
I then traced
the patterns onto 4 pieces (per claw) of 1” thick birch plywood
that I had laying around as scrap from making the knees. (After
looking at some other claws, I think that the stock should be thicker
than 1”, but it is what the pictures here show.) I traced
the front and back of each claw on a separate piece of wood –
it makes the edges match better in future steps.
3) Cut the Claws 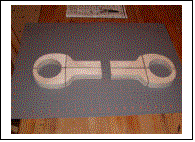
Cut them a little
outside the tracing (especially the inner circle of the claw). You
will sand closer later. Also – mark each piece so that you
can match them up later. I marked the right/left claw front (pincer)
and back (wrist) as well as whether the piece was for the upper
or lower claw. From this point on I did not mix up the pieces. Also,
be sure to mark each piece on the side that faces outward
on the finished robot. This will be very important in future
steps!
4) Sand/Shape the Wrist/Pincer Angle
Using the Disc
Sander (60 grit), set the table angle. I used 15 degrees. Sand both
the “wrist” and “pincer” part of the claws
with the OUTSIDE FACE FACING UP. After sanding,
the wrist portion will have a slight inward angle. The joint ends
will be the same width, but the shape on the top of the two will
not match.
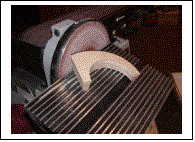
5) Sand/Shape
the Inner Angle
Using the Disc
Sander (60 grit), set the table angle. I used 20 degrees. With the
OUTSIDE FACING UP, sand/shape the inner claw angle
on the pincers (you do not need to sand the wrist pieces). Clean
up and smooth the pieces to meet the tracing. After this step, the
wrist and pincer inner angles should be pretty close.
6) Shape the
narrow end of the pincers.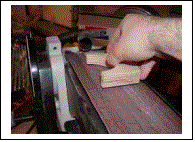
At this point
the pincers of the claws are way too thick at the front. Mark the
width of the tip from the outside face inward. Using the Belt Sander,
carefully sand the pincer WITH THE OUTSIDE FACING UP, being careful
to keep the wrist end of the pincer just above the belt. Work slowly
and carefully. When both the top and bottom of one pincer are close,
compare the width at the tip to make sure that they match.
7) Shape the Tip
The tip of the
pincers will be at an angle. Set the Disc Sander table to 0 degrees
and sand (with OUTSIDE FACING DOWN THIS TIME) until
the tip is rectangular. Your claw will have a flat spot on the front
now, but don’t panic. Carefully smooth the flat spot with
the sander to blend the angles in. I rotated the piece about 1/3
up the pincer with the disc sander, then blended the different angles
on the belt of the belt portion. You might need to hand sand with
a sanding block for final blending. Pincers are done!
8) Glue the
Wrists and Pincers 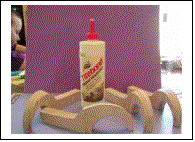
Glue the pincers
and wrist pieces together with wood glue. I though that at I might
want to put a dowel for strength, but tried to break apart a test
claw with the simple butt joints and it did not budge.
9) Match Claw pieces and Sand Inner Claw Hole 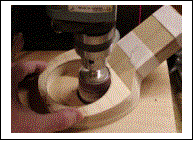
Match the claws
and tape them together in the closed position. Then use a drum sander
attachment (I had one for my drill press) to smooth out the inner
circle so that the hole is round and both the top and bottom of
the claw match. I ended up sanding my circle a little smaller near
the front because of the flat claw tip – I kept working until
it looked right.
10) Sand and Smooth
Smooth out the
edges on the belt sander, putty any nicks with wood filler, and
sand smooth. I reset my bench and drum sanders to 150 grit to get
everything smooth, but it will be smoothed during finishing anyway,
so this was probably not necessary.
DONE!
(except for finishing…)
Ready for Finishing!
This is time
consuming, but not difficult. Take your time and come back to it
if you get bored. I hated this part, and I more than once said “I’d
better just buy a set of claws”. Pride got the best of me,
though, and I persevered…
1)
Seal the claws with a SANDABLE wood primer/sealer.
2)
Skim coat the claw with Bondo Spot and Glazing Putty
according to the directions.
It’s OK
if the coating is not smooth. If you plan to include the “recess”
of the claws, use regular Bondo on the inner holes. Then carefully
sand out the recess with a Dremel tool later You could also use
strips of styrene glued to the inner circle. This is a challenge,
so good luck!
3)
Sand smooth with 320 grit sandpaper, especially
the high spots.
Don’t worry if you sand down to the primer sealer –
You’ll fix it in the next steps. The top claw in the photo
has the first glaze coat. Lower claw is after sanding but before
the second coat.
4) Skim
coat again with Bondo Glazing Putty
5) Sand
high spots with 320 grit paper, then lightly sand with
600 grit to smooth.
6) Prime
with a sandable automotive primer. I used Duplicolor Filler Primer.
7) Sand
according to directions with 400 or 600 grit paper.
8) Fill
any pits with glazing putty.
9) Sand
smooth with 600 grit paper.
10) Prime
again with filler primer and sand if needed. Be picky.
Although the final paint coats of color for the claws will fill
some pits, the high gloss will magnify imperfections.
FINALLY DONE!
Hints and comments? Please send them to me: markweesb9@comcast.net
|