Brain
Construction
By
Steve Tanner
This
is a fairly easy piece to make. The only "hard" part is
cutting out all of the funny little shapes. This is only hard
because it's time-consuming. Even the gluing was a pleasant
surprise.
Materials:
2' x 2' - 1/16" Styrene Plastic Sheet (for the wrap-around
piece, front panel, 2 eye pieces & 2 little spacer pieces)
2' x 4' - 1/4" or 1/8" plastic (preferred) or wood sheet
(top & bottom panels)
1 tube of Plumber's GOOP (Very good adhesive. Sold in most
hardware stores in the same section with the specialty glues like
Krazy Glue. It is NOT in the plumbing section & it doesn't
come in a huge tube like caulk or Liquid Nails. It's approx.
4 oz. tube in a blister pack)
Tools:
Masking tape, Exacto knife, sharp scissors, jig saw or scroll saw,
medium & fine sandpaper (100 and 400 grit) The photo above is
my completed brain section. The little dividers inside were the
first ones I made toisolate the light from the individual bulbs.
I don't believe the original had these, but I preferred the effect
so I went with it.
My
home-made Brain consists of 8 pieces:
- The
top panel & the bottom panel
- The
"wrap-around" panel
- The
front panel
- The
2 "eye" panels
- And
2 little "spacers" between the "eye" panels
& the front panel
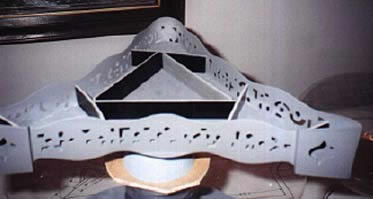
First, make Xerox copies of the Brain section from the blueprints.
(You don't want to cut up the originals, do you?) Take the
copies you made (you probably had to make more than one copy for
the long "wrap-around" piece because of its size if you
did it on a regular copying machine with letter-sized paper) and
cut them out. Note: Cut out the 2 "eye" panels
at the end of the front panel as separate pieces from the front
panel. You'll notice from looking at the bottom & top
plates that they stick out approximately 1/4" from the front
panel. This is where the 2 little "spacers" will
go.
With
an Exacto knife, cut out all the little shapes in the wrap-around
panel, the front panel and the "eye" pieces of your Xerox
copies. These will be your templates.
I'm
going to skip over the boring details of making the top & bottom
panels except to say that you should clamp these 2 pieces together
before you cut them out to ensure they are the same exact size &
shape. I used 1/4" hard board for mine, but in retrospect,
I should have used 1/4" or even 1/8" plastic sheets for
these. The hardboard had to be coated it with fiberglass resin
for a smooth finish. Also, I later changed the top panel to
a 1/8" thick ABS plastic because 1/4" seemed too thick
and it was tough to keep from blocking the many little holes &
not stick out over the top.
The
Wrap-Around, Front & Eye Panels
Tape these templates to the styrene plastic so it is secure.
Trace the entire outlines of these onto the styrene and also trace
all of the little cut-outs. I filled in the little holes (funny
shapes) completely using a ball-point pen.
Remove
the templates and cut out the panels along the outside lines.
They should be fairly easy to cut with a sharp pair of scissors.
Take your time. I used a pair of snips made for trimming bonsai
trees. Once you have these cut out, you will need to
cut out all of the little strange shapes with the Exacto knife.
Place the styrene on a hard surface and carefully cut out the shapes.
This is the time consuming part of the project. DON'T RUSH
IT! Start by pressing very lightly with the blade tip along
the outline, barely making a scratch. Trace over this outline,
gradually sinking the blade deeper until you have cut all the way
through.
I did
mine while watching TV on 3 consecutive nights, so I didn't get
burned out on it & start rushing it along.
The
shapes that are perfectly round are very tempting to drill out.
However, styrene isn't very forgiving with a regular wood drill
bit of more than 1/16" wide. It tends to rip as the bit
starts to take hold. (Trust me on thisÖI ruined my first
attempt with a drill!) I didn't try any different types of
bits (like masonry bits) and it might even be better to hot glue
the styrene to a piece of wood to keep it in place and held down
securely while drilling. Definitely a low speed & light
pressure should work best.
A better
method, since small, round holes are very difficult to cut with
an Exacto knife, is to use a hole punch. Some of the circles
are larger than the standard 1˜4" punch and they are also beyond
the reach of the punch head. I was fortunate that where I
worked, we had a punch that resembled a drill press with interchangeable
punch heads. Most local commercial printing companies (and
even copy shops) have this type of drill. They may, however
shy away from using it on plastic. However, I used ours with
no dulling of the bits at all. Styrene is a pretty soft plastic.
Cut
out the front panel, wrap-around panel and the 2 eye pieces in the
same way.
Once
these are completed, you will attach the wrap-around piece to the
bottom panel. Dave's drawings show the center line & where
the wrqap around pieces meet the top & bottom panels. Mark the
center line of the wrap-around panel and the center of the rear
point of the bottom panel so you can line them up properly.
MAKE
SURE YOU HAVE THE WRAP-AROUND & FRONT PANEL RIGHT SIDE UP SO
ALL OF THE LITTLE HOLES ARE WHERE THEY ARE SUPPOSED TO BE!
Draw
a line straight across the inside of the wrap-around piece.
Make the line run the entire length of the piece, so it will serve
as a guide to make sure the bottom panel is level. The way
I did this is as follows: I laid down the wrap-around piece
with the side that will be on the inside facing up. Using
a straight edge, draw a line that is just below the lowest of the
funny-shaped cut-outs. You don't want the bottom panel to block
any of these openings! Use this line to make sure you have
the correct position when you glue the wrap-around to the bottom
panel.
**When
applying the GOOP, try not to get it all over the place & wipe
off any excess. It can be a problem later when you're finishing
& painting.
I later
thought that it may have been easier to use contact cement for this.
Apply the contact cement to each surface until tacky, then join
the surfaces. It will be strong and won't need to be taped
to hold it together because there's no real "drying time".
You could try this method and reinforce the seam on the inside with
a bead of GOOP later. I haven't tried this, but it should
work.
I started
gluing the wrap-around at the center of the back (where you marked
the lines). I put a bead of Plumber's GOOP all the way around
the back point of the bottom panel, running about 1" along
the length of the side on each side. I placed the wrap-around
against the bottom panel and held it in place for about 5 minutes.
When it seemed it was OK to let go, I carefully applied some masking
tape to hold it in place, being careful not to move it.
Once
it's fairly secure, start applying GOOP all the way around to the
front of the bottom panel. Press the wrap-around in place, securing
it as you go with masking tape. Keep checking your alignment
against the line you drew on the inside of the wrap-around.
Once
the entire wrap-around is in place, allow the GOOP to set (at least
a few hours) before moving on.
Now
you're ready to mount the front panel. Pretty straight forward.
Draw a line on the back (or inside) as you did for the wrap-around
for alignment. Now, GOOP it in place. Now, you should
see what's next. Yup, glue the "eye" pieces in place.
For
the little gaps between the front panel and the "eyes",
cut two little strips of styrene plastic and glue them into the
gaps. All of the seams between the pieces can be filled with
a little Bondo or Bondo Spot & Glazing Putty. Probably
best would be plumber's epoxy putty because it adheres to plastic
very well. I learned of this material from B9 Club & R2-D2
Club member, Vince Roberts, unfortunately after most of my parts
were completed. It's very strong, sticks to just about anything
and is easily sanded & shaped. (Thanks, Vince!)
On
the underside of the bottom plate, you may opt (as I did) to fill
the joint where the wrap-around panels attach to the plate.
I did this with a little Bondo Glazing Putty, applied with my fingertip.
Apply just enough to get it into the cracks since it won't stick
well to the flat surfaces. Plumbers epoxy putty should do
this job better, too. Other types of caulks (like sandable
& paintable silicone caulk) may work well, but I have not tried
them.
The
top panel just sits inside the wrapped panels on top of either small
wooden blocks or (like mine) on top of the little light dividers.
Gravity is all that's needed to hold it in place.
Lightly
sand, prime & paint, then stand back and marvel at the great
job you've done! Total cost is about $12 and about 20 hours
of time.
|